As a company tasked with checking and refilling stock levels for a number of clients, you have a huge responsibility. The future of your business relies on keeping clients sufficiently supplied, while managing your own stock levels. It can be a constant juggling act. And, currently, it’s one that’s not helped by technology as much as it could be. When much of the monitoring, both on-site and off-site, is done in person, the room for error is huge. Misread stock levels and the result can be hugely damaging from both a reputational and financial standpoint. But some organizations, from industrial plants to manufacturers, aren’t settling for the status quo. Suppliers on the cutting edge of technology are implementing the IoT into their operating processes to revolutionize the way in which they monitor, manage and refill client stock levels.
THE PROBLEMS FACING OFF-SITE SUPPLIERS AND MANUFACTURERS
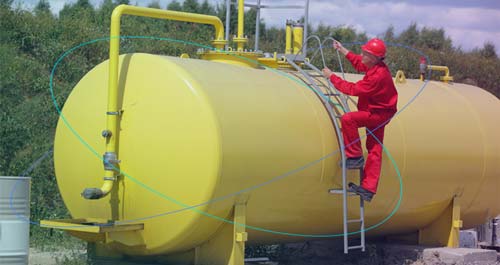
When plants, manufacturers, and suppliers check stock levels by hand, they run into a series of problems. Sending out employees to check on client stock levels is hugely inefficient and often a complete waste of company resources. Worse still, everyone is prone to human error and a misreading of stock levels can result in losing the client. The round trips that employees have to make quickly add up. That’s not to mention the expensive emergency deliveries that need to be carried out when a client’s stock levels fall too low. This can add a significant amount to your company’s bottom line costs but also to its carbon footprint. Constant trips are hardly good for the environment. Predicting client stock levels also becomes an exercise in futility. With no way to accurately know how much the client is regularly using, trying to predict when they might run out is like shooting in the dark. There’s no way of knowing if you’re going to be right. All this makes the job of providing a reliable service incredibly difficult. It’s no surprise that losing clients is a common problem.
SMART SUPPLIERS TURN TO THE IOT FOR HELP
Manufacturers, industrial plants and suppliers no longer have to rely on manual labor to monitor client storage levels and predict refill schedules. IoT can now do all of this work for them. This is all made possible by remote wireless monitoring devices that can be installed within client storage tanks both on-site and off-site. These devices, which can be installed in minutes without additional wiring, remotely send data via the Sigfox network to an online dashboard that can be accessed from anywhere in the world on practically any device. This allows staff to remotely monitor storage levels across their clients at a click of the button without completing expensive round trips. It also means that companies can receive accurate up-to-the-minute data that they can use to predict refill schedules and create a more efficient business model.
Because the devices run on Sigfox’s Low Power Wide Area Network (LPWAN), they are both long lasting and incredibly reliable. Devices sending data over the Sigfox network use very little power to send it to the cloud, which means that very little battery power is used up. As a result, the devices will have both a long and very predictable battery life. Ongoing subscription fees are also low as a result of the low-power nature of the network, allowing the small investment to deliver huge ROI.
Ultimately, the IoT devices help companies deliver a markedly more reliable service and should, if used correctly, mean that expensive emergency deliveries become a thing of the past. Consequently, companies will be able to significantly reduce their carbon footprint as well as retain more clients and forge stronger supplier-client relationships.